Tata Steel Packaging in Duffel (Belgien) hat ein einzigartiges Schutzsystem in seiner Protact®-Produktionslinie für Verpackungsmaterial installiert. Das für die Qualitätssicherung bestimmte System wurde in enger Zusammenarbeit mit TCS entwickelt. Die TCS-Ingenieure ließen sich dabei von so unterschiedlichen Anlagen wie Reinräumen und Konzertzelten inspirieren.
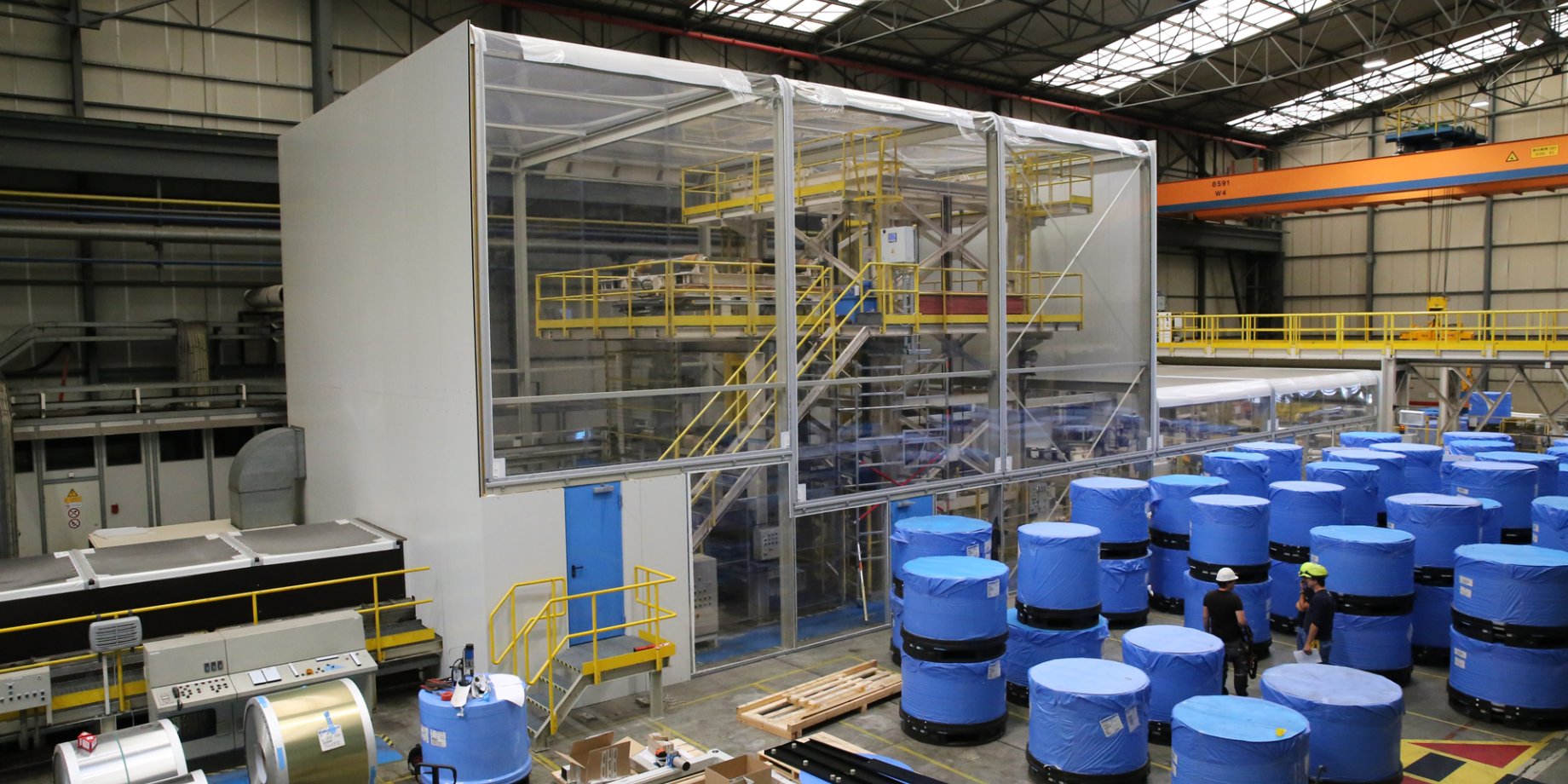
Einfassung der Protact®-Produktionslinie
Protact® ist das von Tata Steel patentierte lebensmitteltaugliche Material, das bei der Herstellung von Dosen für Lebensmittel, Getränke und Aerosole verwendet wird. Es besteht aus einem Stahlsubstrat, das beidseitig mit einer dreilagigen Polymerbeschichtung beschichtet ist. „Das Material ist eine herausragende Alternative zu lackiertem Stahl und wird wegen seiner Effizienz in der Produktion und seiner Branding-Flexibilität geschätzt“, sagt Jan-Willem Vos, Site Manager des Standorts Duffel von Tata Steel. „Das Material wurde um die Jahrtausendwende erfunden und hat nach und nach einen immer größeren Marktanteil erworben, besonders seit 2009.“
Schutz vor Verschmutzung
Allerdings hatte der Erfolg auch seine Schattenseiten, da mit den steigenden Produktionsvolumen einige Qualitätsprobleme auftauchten. „Wir haben festgestellt, dass die dreilagige Beschichtung an einigen Stellen löchrig sein konnte, was zu einer deutlich höheren Ausschussquote bei unserer internen Qualitätskontrolle führte - ganz besonders im Sommer“, erklärt Vos. „Bei den Analysen stellte sich heraus, dass das Problem durch verschiedene Verschmutzungen ausgelöst wurde, die sich vor der Beschichtung auf dem Stahl festsetzten. Dabei konnte es sich um winzige Sandkörner, Feuchtigkeit oder Insekten handeln. Wir mussten herausfinden, wie wir unsere Produktionslinie besser gegen Insekten und andere Verschmutzungsquellen abschotten könnten.“
Die Suche nach einer praktikablen Lösung
Es wurden Tests mit einer zusätzlichen Schutzstruktur durchgeführt. Peter Borremans, Technical & Process Manager, erläutert: „Wir haben eine Struktur um die Produktionslinie aufgebaut, um den Prozess sozusagen einzuschließen. Die Ausschussquote ging beinahe sofort auf ein annehmbares Niveau zurück. Dies bewies unsere Annahme, aber die Lösung war langfristig nicht tragbar, da die Struktur sich negativ auf die Arbeitsbedingungen auswirkte und voraussetzte, dass wir zusätzliche Beleuchtung installieren und weitere Sicherheitsvorkehrungen treffen. Außerdem erschwerte sie die Wartungs- und Reinigungsarbeiten ganz erheblich. Was wir also brauchten, war eine transparente Struktur, die schnell auf- und wieder abgebaut werden konnte.“
Die Qualität ist dank der besseren, abgedichteten Einrichtung erheblich besser, und die Reinigungs- und Wartungsarbeiten können mühelos organisiert werden
Konzertzelte als Inspirationsquelle
Borremans wusste, dass er eine nachhaltige Lösung nicht ohne Hilfe entwickeln konnte. Die Suche nach einem Partner stellte sich jedoch als recht schwierig heraus. „Verschiedene Unternehmen unterbreiteten Vorschläge, die jedoch alle zu kurz griffen, vor allem da die Installation und Demontage zu aufwendig geworden wäre. Dann kamen die Leute von TCS mit ihrer Idee. Sie schlugen vor, sich von Konzertzelten inspirieren zu lassen - von einem Bereich also, in dem sie wertvolle Erfahrungen durch die Zusammenarbeit mit dem Konzertbühnenentwickler Stageco gesammelt hatten. Wir fanden den Vorschlag von TCS überzeugend, daher arbeiteten wir eng zusammen, um dieses transparente, modulare, leichte und benutzerfreundliche System zu konzipieren und zu entwickeln, das genau auf unsere Bedürfnisse zugeschnitten ist.“
Faszinierend, wie gut es funktioniert
Das als TEPE (Total Enclosed Protact® Environment) bekannte System besteht aus einem modularen Stahlrahmen mit transparenten, flexiblen Plastikfolien, die leicht installiert und wieder abgenommen werden können. Das 12 Meter breite und 10 Meter hohe System schützt die Produktionslinie über eine Länge von 40 Metern, ohne unerwünschte Nebenwirkungen. Borremans bestätigt. „Die Arbeitsbedingungen sind viel besser als mit der alten Einrichtung. Nun hat jeder einen perfekten Überblick des gesamten Prozesses. Die Qualität ist dank der besseren, abgedichteten Einrichtung erheblich besser, und die Reinigungs- und Wartungsarbeiten können Zone für Zone schrittweise organisiert werden, was die Produktionsstillstandzeiten minimiert. Faszinierend, wie gut es funktioniert! Ich bin sicher, dass diese Lösung auch in anderen Produktionsumgebungen Einzug halten wird.“