Tata Steel Packaging à Duffel a installé un système de protection unique sur sa ligne de production pour le matériau d’emballage Protact®. Le système améliore la qualité du produit et a été développé en étroite collaboration avec les ingénieurs de TCS, qui se sont inspirés de diverses constructions, comme les cleanrooms et les tentes de concert.
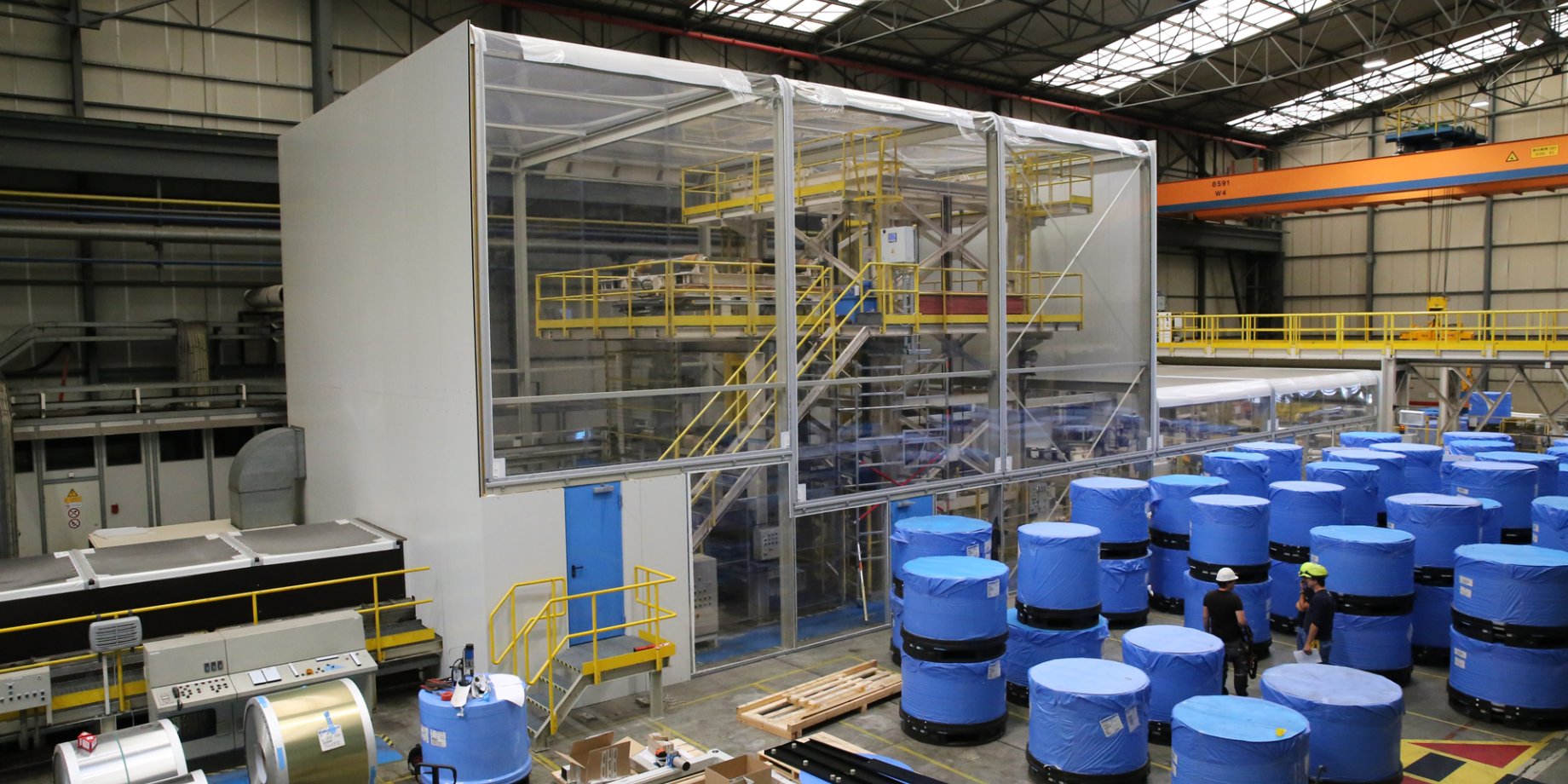
Confinement de la ligne de production Tata Steel Protact®
Protact® est le matériau répondant aux exigences de sécurité alimentaire breveté par Tata Steel qui est utilisé dans le cadre de la production de conserves alimentaires, de boissons et d’aérosols. Il se compose d’un support en acier, avec de chaque côté un revêtement consistant en 3 couches de polymères. « Le matériau est une excellente alternative à l’acier laqué, extrêmement apprécié pour son efficacité de production et sa flexibilité d’utilisation élevée », déclare le Site Manager de Tata Steel Duffel, Jan-Willem Vos. « Le matériau a été développé au tournant du siècle et a progressivement acquis une part de marché importante, en particulier depuis 2009 ».
Protection contre la contamination
Mais toute médaille a son revers, de sorte que l’augmentation des volumes de production a généré quelques problèmes de qualité. « Nous avons constaté que le revêtement à trois couches pouvait être perforé à certains endroits, créant une hausse significative du taux de rejet lors du contrôle de qualité interne, en particulier pendant la saison estivale », explique Vos. « Une analyse a permis de démontrer que le problème était causé par la contamination de l’acier avant l’application du revêtement. Il pouvait s’agir de minuscules grains de sable, d’humidité ou d’insectes. Nous devions clairement trouver une façon de mieux protéger notre ligne de production des insectes et d’autres sources de contamination. »
Recherche d’une solution viable
Des tests ont été réalisés à l’aide d’une structure de protection auxiliaire. Le Technical & Process Manager Peter Borremans précise : « Nous avons construit une structure autour de la ligne de production pour, en quelque sorte, emballer le processus. Le taux de rejet a presque immédiatement diminué pour atteindre des niveaux acceptables. L’analyse s’est donc révélée correcte mais la solution n’était pas viable à long terme vu que la structure avait un impact négatif sur les conditions de travail, nous contraignant à installer un éclairage supplémentaire et à prendre des mesures de sécurité additionnelles. Cela compliquait en outre fortement la maintenance et le nettoyage. En réalité, ce dont nous avions besoin, c’était une structure transparente qui pouvait être montée et démontée rapidement. »
La qualité a augmenté de manière significative en raison de l’amélioration de l’étanchéité de l’installation, et le nettoyage et la maintenance peuvent être organisés facilement
Des tentes de concert comme source d’inspiration
Borremans savait qu’il ne pouvait pas développer une solution durable sans aide extérieure. Cependant, la recherche d’un partenaire adéquat s’est avérée relativement difficile. « Diverses sociétés ont soumis des solutions mais aucune ne s’est révélée satisfaisante, généralement parce l’installation et le démontage étaient trop fastidieux. Mais TCS est alors arrivée avec une idée. Ils ont proposé de s’inspirer des tentes de concert, un domaine dans lequel ils avaient acquis une précieuse expérience grâce à leur collaboration avec Srageco, un développeur de scènes de concert. La proposition de TCS nous a convaincus et nous avons donc collaboré étroitement en vue de concevoir et de développer ce système de protection transparent, modulaire, léger et facile à utiliser, parfaitement adapté à nos besoins. »
Une efficacité impressionnante
Baptisé TEPE (Total Enclosed Protact® Environment), le système consiste en un cadre en acier modulaire avec des bâches en plastique flexible transparent qui peut être installé et retiré facilement. Avec une largeur de 12 mètres et une hauteur de 10 mètres, il protège la ligne de production sur une longueur de 40 mètres, sans effets secondaires indésirables. « Les conditions de travail sont bien meilleures qu’avec l’ancien système ; tout le monde a désormais une vision parfaite de l’intégralité du processus. La qualité a augmenté de manière significative en raison de l’amélioration de l’étanchéité de l’installation, et le nettoyage et la maintenance peuvent être organisés zone par zone, réduisant ainsi les temps d’arrêt à un minimum. Le système présente une efficacité impressionnante. Je suis certain que la solution sera également intégrée dans d’autres environnements de production, » confirme Borremans.