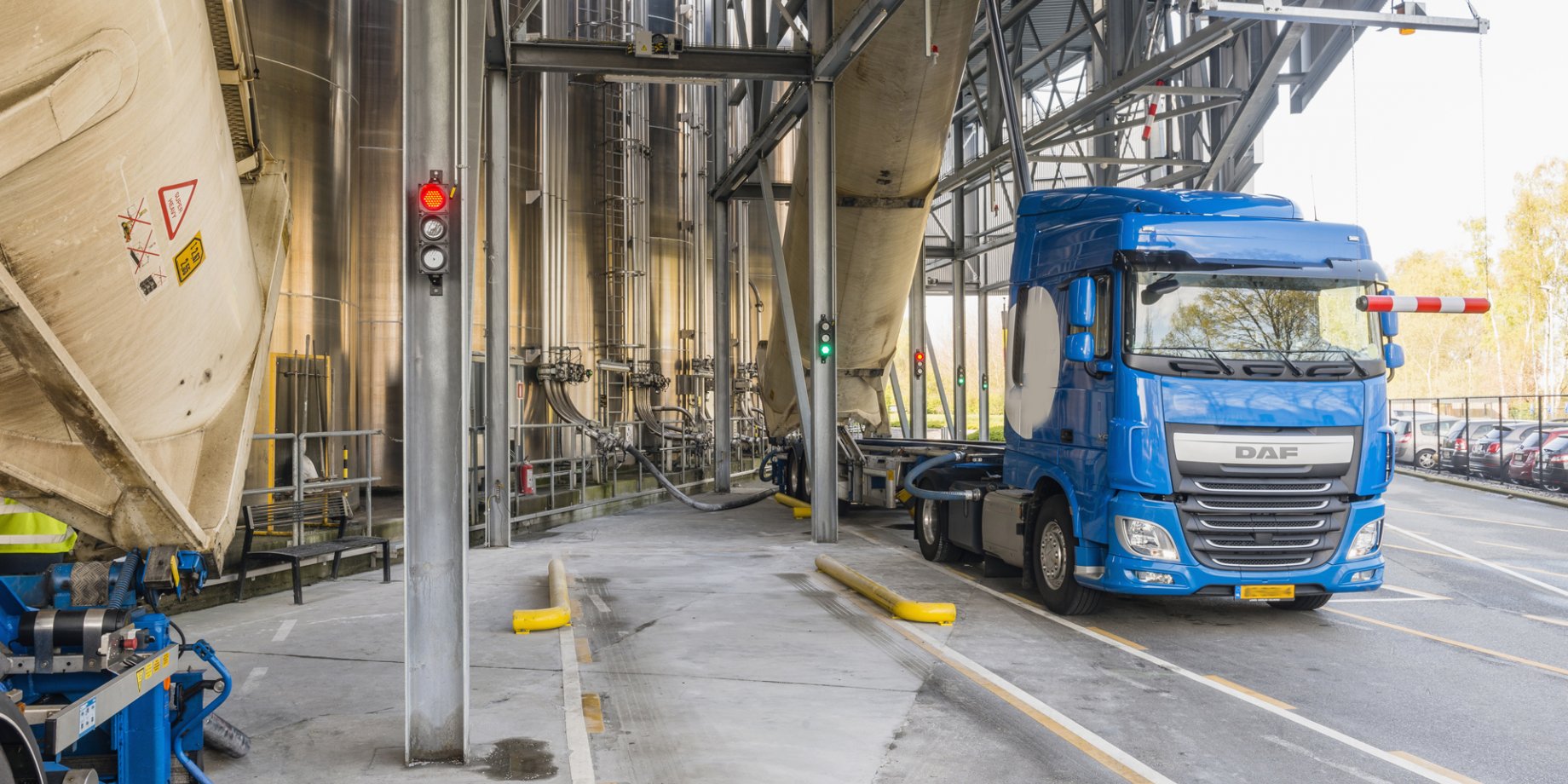
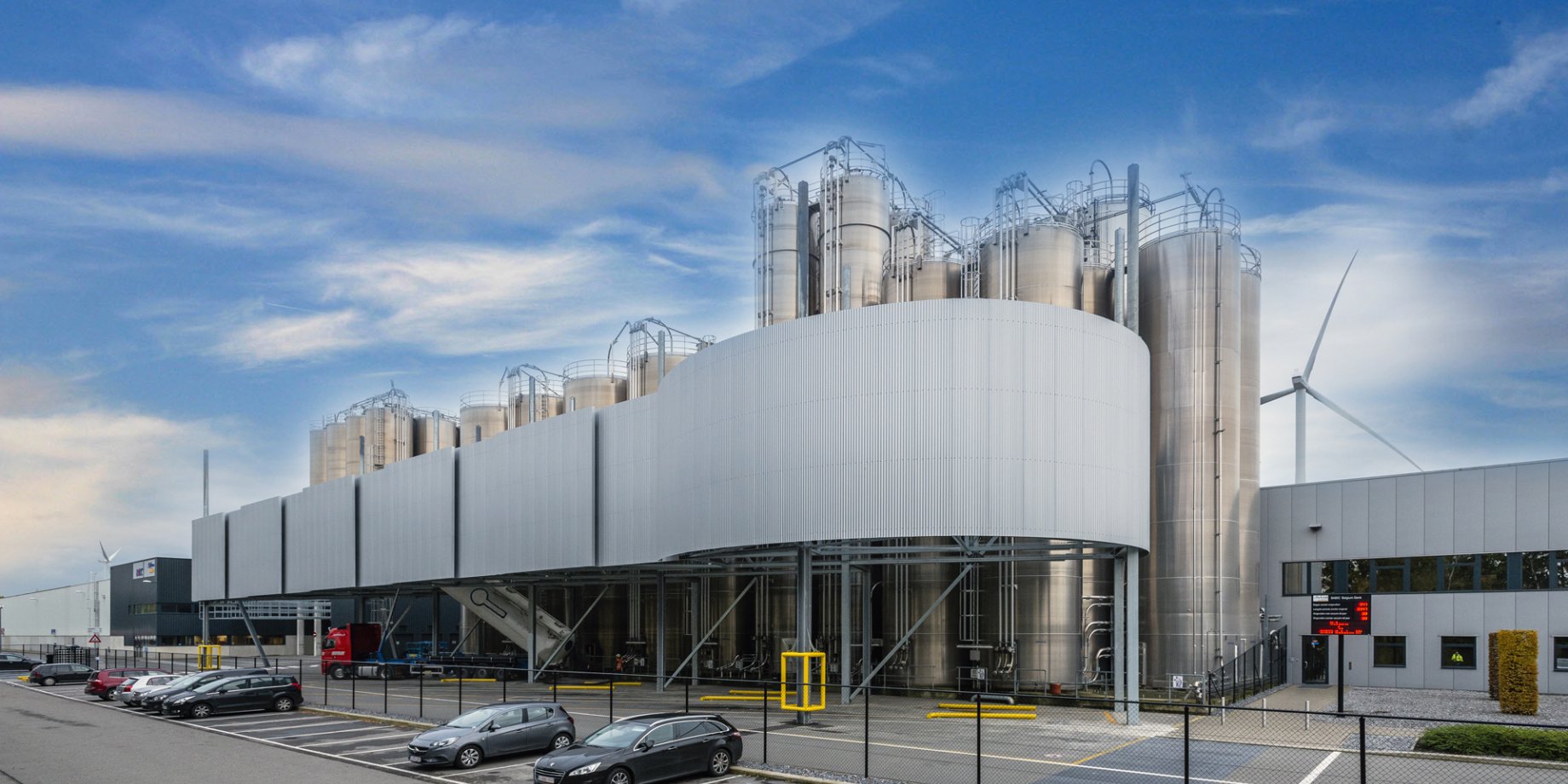
Een slim project dat de veiligheid verbetert
De Sabic-fabriek in Genk produceert polypropyleenverbindingen, vooral voor de Europese automobielmarkt (zie ook ‘Sabic’). In dat proces worden polypropyleenpellets gemengd met verschillende materialen, waaronder rubber en glasvezel. De grondstoffen worden continu aangevoerd in bulk- of containertrucks aan een gemiddeld tempo van zowat tien vrachtwagens per dag. De bulkloskade is al jaren ingericht conform de strengste veiligheidsnormen, maar ondanks dat, gebeurde er enkele maanden geleden een ongeval waarbij een truck zijdelings omkantelde en de chauffeur ernstig gewond raakte. “Veiligheid is onze topprioriteit, dus het ongeval heeft ons aangespoord om het hele proces van materiaal lossen kritisch te evalueren,” zegt Sabic Projectmanager Stefan Gielen.
Bijkomende fysieke barrière nodig
Voorafgaande analyses toonden aan dat dit incident minder ongewoon was dan eerst gedacht. “We stelden vast dat er in Europa gemiddeld één incident per maand is met trucks die tijdens het lossen kantelen,” zegt Gielen. “Dat kan bijvoorbeeld gebeuren als de container niet goed is vastgemaakt of misschien door een plotse windstoot. We hebben die incidenten geanalyseerd en besloten dat er een bijkomende fysieke barrière nodig is om dergelijke incidenten volledig uit te sluiten.”
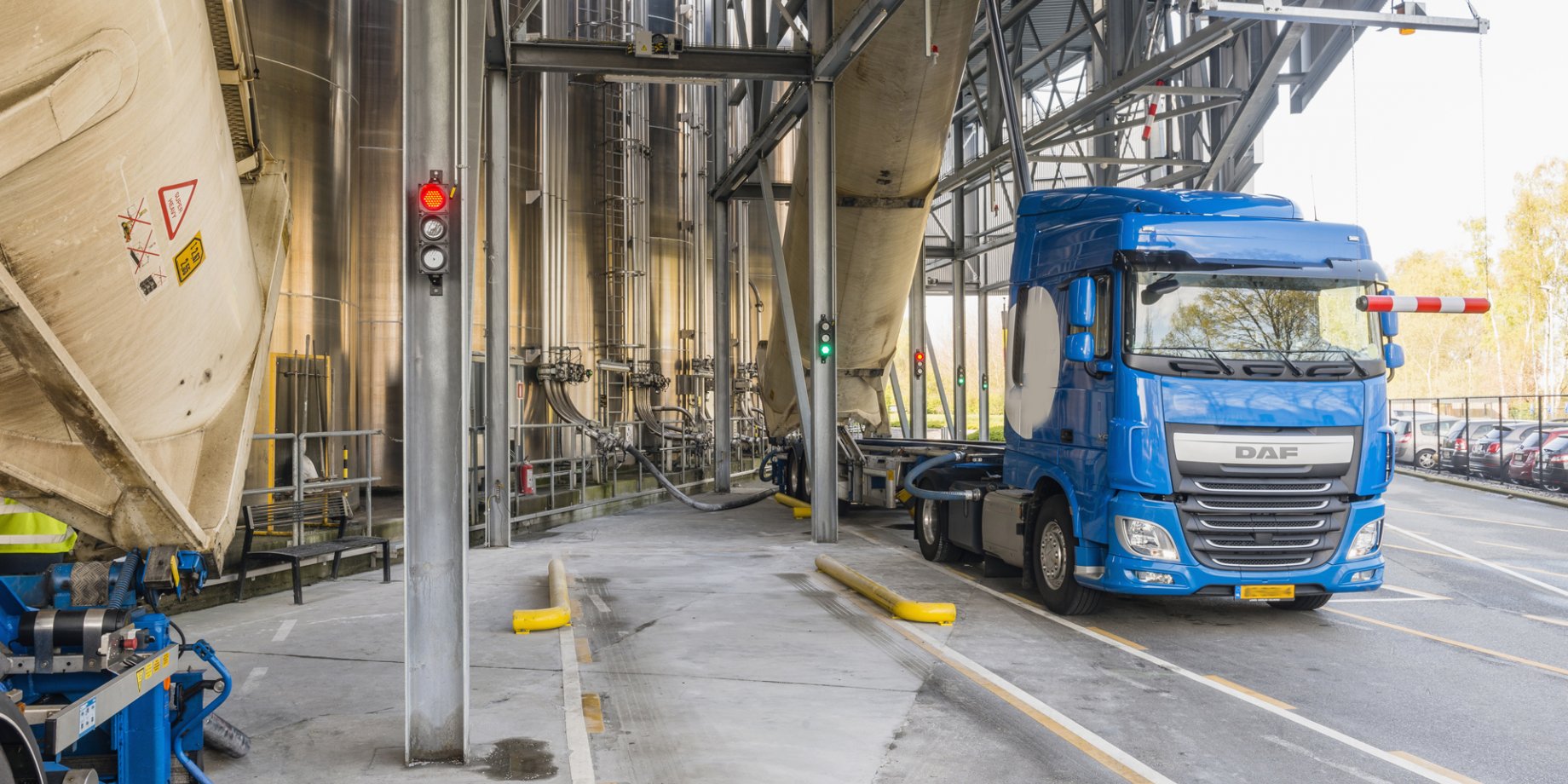
Weinig manoeuvreerruimte over een grote oppervlakte
Sabic had een dergelijke oplossing gezien tijdens een technisch bezoek aan een ander bedrijf in Nederland. “Het idee was om een robuuste stalen structuur te bouwen boven de losplaats,” vertelt Gielen. “Als de truckcontainer omhoog gekipt is in lospositie werkt die structuur als een kooi, waardoor zijdelings bewegen niet mogelijk is. Het is een eenvoudig idee maar we zagen meteen dat er slim ingenieurswerk bij zou komen bij kijken om het te doen werken, zeker gezien de beperkte manoeuvreerruimte van de trucks en de grote oppervlakte van de losplaats.”
Scanners, signalisatie en alarmen
In een eerste projectfase werd de technische oplossing ontwikkeld: “We wilden een staalconstructeur met eersteklas adelbrieven in engineering,” zegt Gielen. “Daarom huurden we TCS in, ook omdat ze ervaring hebben met zowel uitdagende staalconstructies als met de interne logistiek op industriële sites. We organiseerden vergaderingen met twee van onze belangrijkste leveranciers om enkele losscenario’s te ontwikkelen en te testen. De scenario’s werden geëvalueerd op technische en organisatorische haalbaarheid en bovenal op veiligheid. We beslisten onder meer dat de structuur moest uitgerust worden met een veiligheidssysteem om botsingen te vermijden. Dit systeem moest robuust zijn en kunnen werken met trucks van uiteenlopende lengtes en met verschillende wielbases. De ingenieurs van TCS ontwikkelden hiervoor een praktische oplossing met laserscanners om de positie van de truck te bepalen, signalisatieapparatuur en auditieve alarmen.”
Effectief en comfortabel
Uiteindelijk heeft TCS het project ook uitgevoerd. Gielen: “We hebben verschillende firma’s om een offerte gevraagd, maar we waren het meest overtuigd door TCS, zeker gezien hun benadering van de veiligheidsproblematiek en hun slimme organisatie van de werkzaamheden. Die moesten immers plaatsvinden op een site in volle activiteit.”
De bouw werd gestart in mei 2015 en is op twaalf weken tijd voltooid. Het project is een succes geworden. “Onze truckchauffeurs zijn er heel blij mee,” zegt Gielen. “Ze bevestigen dat het systeem goed werkt en hebben nog geen ongemakken gerapporteerd. Integendeel: ze zijn blij dat ze nu onder een dak kunnen werken, dat is veel comfortabeler dan vroeger.”
Scenario's voor het lossen werden geëvalueerd op technische en praktische haalbaarheid en op veiligheid.
Sabic
Sabic is een bedrijf met hoofdzetel in Riyad in Saoedi-Arabië en behoort tot de grootste petrochemische producenten ter wereld. 70% van de aandelen zijn in handen van de Saoedi-Arabische regering en de overige 30% zijn van privéinvesteerders in Saoedi-Arabië en de andere vijf landen van de Gulf Cooperation Council. Sabics eenheden voor productie, verkoop en innovatie zijn verspreid over de hele wereld en worden beheerd vanuit vier regionale kantoren: het Midden-Oosten en Afrika, Azië, Noord- en Zuid-Amerika en Europa. De eenheid in Genk produceert polypropyleenverbindingen en het gepatenteerde product Stamax, een glasvezelversterkte kunststof.
Specificaties
Staalstructuur:
- 600 m² loskade met vijf losplaatsen.
- Hoogte 12 m.
- 70 ton structureel staal.
Veiligheidssysteem:
- Laserscanners op elke losplaats registreren de exacte positie van de truck terwijl die achteruit in de losplaats rijdt.
- Verkeerslichten signaleren de huidige positie, van groen (binnenkomend) over oranje (naderend) en flikkerend oranje (dicht bij doel) tot rood (aangekomen).
- Zodra de truck op de juiste positie staat, kan het kippen beginnen. Een bijkomende scanner detecteert de kippositie en activeert een gevaarteken dat voor de truckcabine wordt neergelaten. Dit is een waarschuwing aan de chauffeur dat hij niet mag rijden.
- Eens de container terug horizontaal ligt, wordt het gevaarteken automatisch opgetrokken, het signaal aan de chauffeur dat het veilig is om de losplaats te verlaten.