Demand for custom-made precast moulds and flexible formwork systems is on the rise as a result of the increasing complexity of concrete construction projects. This is illustrated by Construx, a leading formwork manufacturer whose moulds and formwork systems are used in projects around the world. “Solid engineering capabilities are needed to meet today’s challenges.”
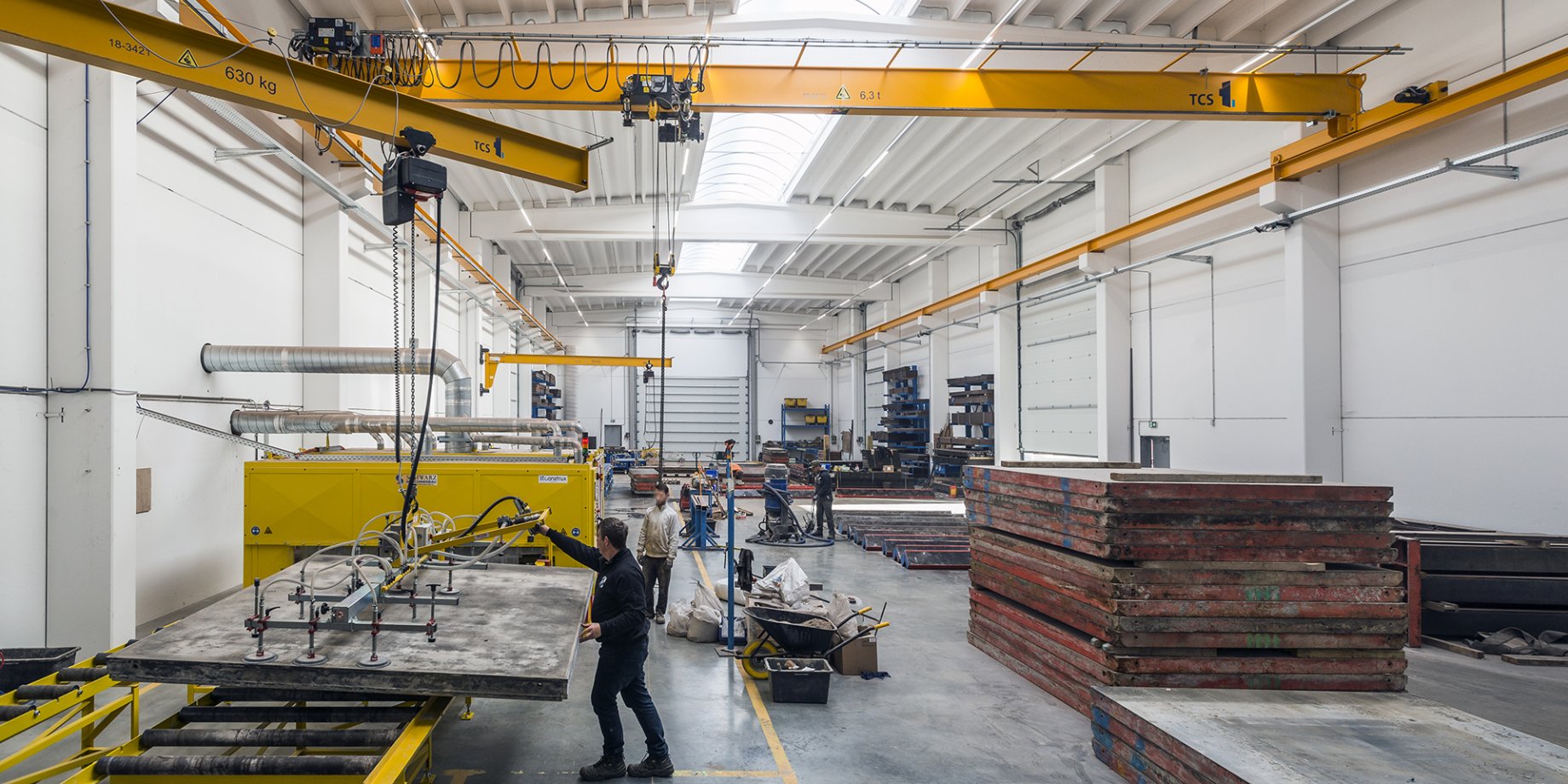
Dealing with peculiar geometries
Bart Meermans, Plant Manager at Construx Genk, outlines the trend: “The evolution towards ever more spectacular architecture and civil engineering projects has been going on for many years now. Today, oddly shaped creations are not so exceptional anymore, they’ve become almost mainstream. And when it comes to concrete structures, there’s a general rule: the more spectacular the construction, the more complex the formwork.”
Involved early in the project
This is why Construx over the years has developed robust inhouse engineering expertise, in line with their motto ‘Shaping the Future of Concrete’. “We increasingly need to develop complex, custom-made formwork solutions, either for precast plants or for onsite construction work. This means we get involved early in the project to develop the most appropriate formwork solution for the project in hand. Bear in mind that formwork design and functionality can have a significant impact on construction speed, the timing of project activities and overall project costs. Construction companies greatly appreciate the fact that we have the right people on board to help them optimize their work.”
Formwork design and functionality can have a significant impact on overall project costs
Odd geometries presenting challenges
A recent example of a complex architectural shape built using Construx formwork is Antwerp Province’s new main office, a distinctive 14-storey structure with a twisted outline and a remarkable pattern of triangular windows cast in situ using white fair-faced concrete. Meermans: “The odd geometry and the very dense reinforcement presented a tough challenge. We designed an adjustable and twistable steel formwork with no tie-bars through the walls, and the inside panels have a stainless steel facing to avoid rust stains. We’ve been working closely with the construction company to optimize the formwork and develop an effective casting procedure.”
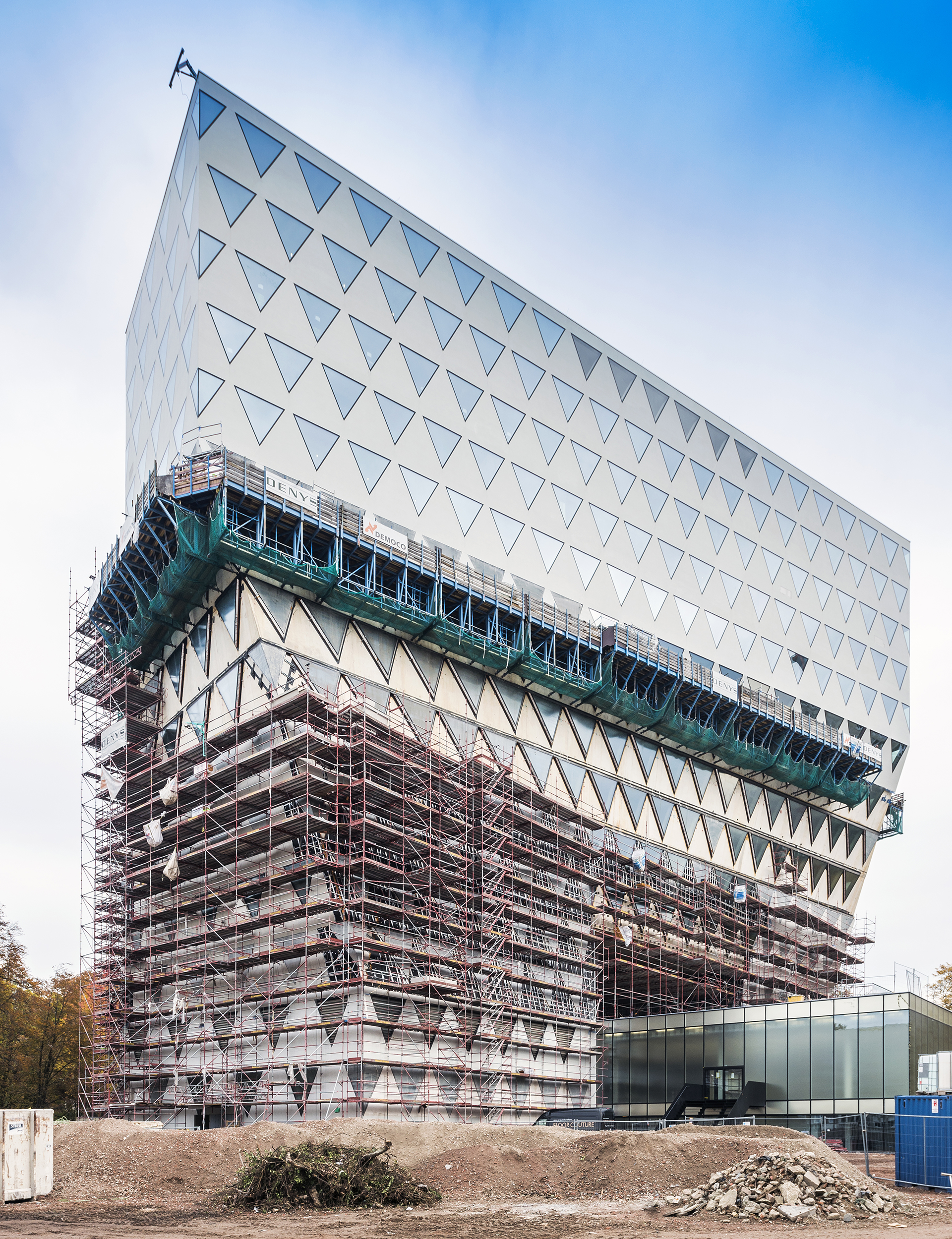
Fascinating projects and products
Other fascinating projects using Construx formwork solutions can be seen on the www.construx.be website. Examples include the LUAS light rail line viaduct south of Dublin, Ireland, the A4 Kethel tunnel in the Netherlands city of Delft, quay walls made from prefabricated blocks in Tema Port in Ghana, the new Ghent railway station platforms in Belgium, and standardized bridge arches over the Belgian Infrabel national rail network, among many others. An eyecatcher is the Combicaster multifunctional stair mould developed for a German company, allowing fast in situ casting of any type of winding staircase.
New cleaning and repair shop to improve service
In addition to customized solutions, Construx also supplies standard formwork systems including a wide variety of standard precast moulds. The company also offers a steel and aluminium shuttering rental service where sufficient panels must always be in stock to be responsive to customer needs. Returned panels also have to be cleaned, and if necessary repaired, as quickly as possible. To achieve this, Construx recently built a new workshop in Genk with an automated panel cleaning line and a repair area. TCS developed and installed the workshop’s comprehensive array of lifting equipment, which includes an overhead crane, two jib cranes and appropriate vacuum lifters. Meermans praises the collaboration: “They did more than just give us the tools we asked for. For example, they suggested to attach the jib cranes to the building structure instead of delivering standalone jib cranes. This turned out to be much more effective than our original idea.”
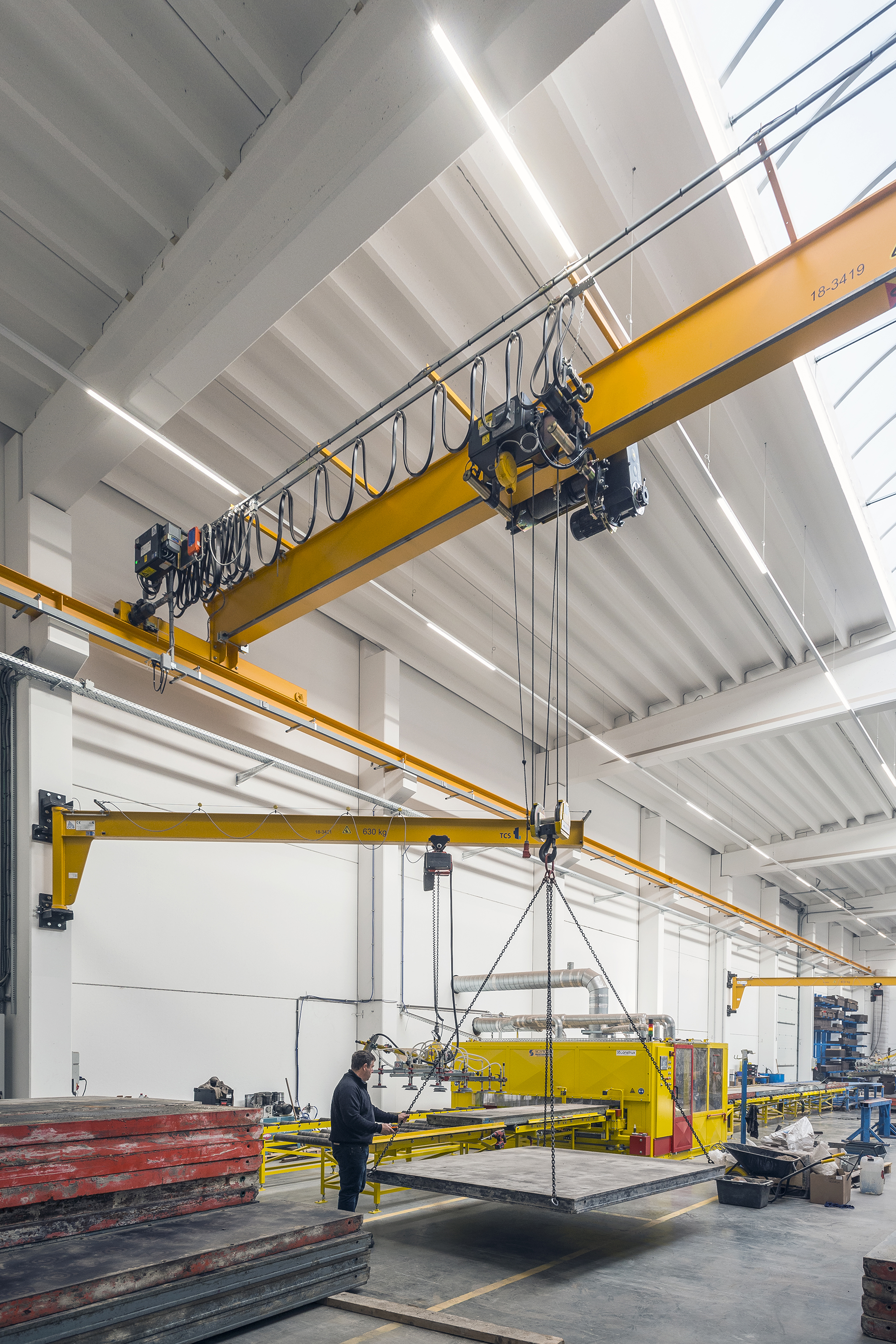
Specifications
- EBK 6.3-tonnes 16.7-metre overhead crane with frequency control
- Two 630-kg 6-m jib cranes
- Two 500-kg vacuum lifters to be used with the overhead and jib cranes
Inspired by this story?