Agro-industrial group Siat has modernised its Presco PLC palm oil mill near Benin, Nigeria. Productivity, quality and reliability significantly increased when tilting sterilisers were installed, the latest advance in fresh fruit sterilisation. The project also results in a marked decrease in effluent production and greenhouse gas emissions.
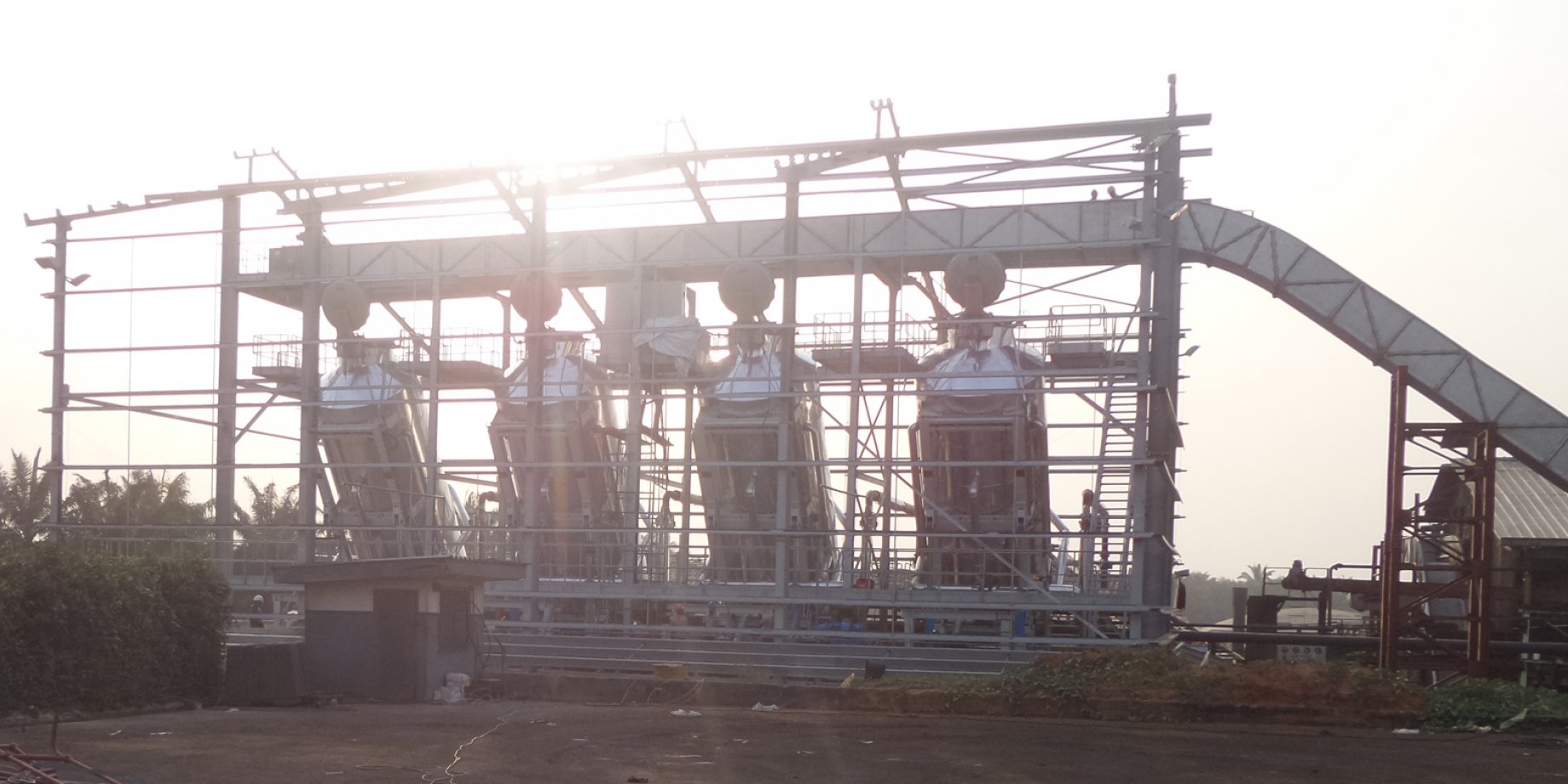
Upgrading the palm oil mill
Siat is a Belgium-based group of companies specialising in the setting-up and management of plantations in the tropics as well as related processing and downstream industries. Their main focus is on the production of palm oil and rubber, with cattle ranching also gaining in importance. Siat is active in Nigeria, Ghana, Gabon, Ivory Coast, and Cambodia, and is currently extending its operations to the USA and China. With environmental and social responsibility being key elements in the group’s strategy, Siat is always looking for ways to improve production to the benefit of staff, shareholders, business partners, consumers, and the world-wide economies in which it operates.
The most critical stage
One recent project involved the installation of a bank of tilting sterilisers at the Presco PLC palm oil mill in Nigeria. Project manager and mechanical engineer Anthony Cornelius explains why this project was so important: “The sterilisation of the fruits is the first and most critical stage of the palm oil processing cycle. Sterilisation is done by cooking the incoming fresh fruit bunches at a temperature of 134°C in a humid environment at a pressure of 3 bar. This must be done in a very controlled way, since improper sterilisation seriously affects the efficiency of the subsequent stages of threshing, digesting and purifying.”
The sterilisation of the fruits is the first and most critical stage of the palm oil processing cycle
Inefficiency of traditional sterilisation
Traditionally, sterilisation has been done in a giant steriliser installation accommodating a series of 2.5 tonnes cages filled with fresh fruit bunches. However, this system was rather inefficient. Cornelius explains: “Space usage inside the cages was suboptimal compared to, for instance, a cylindrically-shaped space, which led to excessive steam consumption. In addition, bobcats were needed to push the cages into the steriliser, capstan arrangements were needed to withdraw them afterwards and further manipulations had to be done using hoisting equipment. This was a laborious and energy-intensive process.”
Best of both worlds
The drawbacks of horizontal sterilisation systems have led the industry to develop vertical cylinder-shaped sterilisers, which are filled at the top via conveyors. This has increased efficiency and produced considerable savings in steam for every tonne of fruit. However, the extra weight of a vertically arranged system causes the oil in the lowermost bunches to be pressed out, resulting in oil loss and hence reduced productivity. “And that’s why tilting sterilisation was developed,” says Cornelius. “It is in fact a smart compromise between horizontal and vertical sterilisation. The steriliser vessel is raised into a near-vertical position for filling, lowered to a horizontal position for sterilisation, then raised again to discharge the bunches into the thresher.”
A tilting steriliser is a vessel which is raised to a near-vertical position for filling, lowered to a horizontal position for sterilisation, and then raised again for discharging.
Benefits already apparent
Four tilting sterilisers have been installed at Presco PLC, and the process flow was modified and streamlined as a result. This required the construction of a steel superstructure (see ‘High expectations fulfilled’) to accommodate the sterilisers and related equipment, including two input and three output conveyors, a chute with autoloaders, a condensate pit with a chimney and an electrical control panel and hydraulic pack. The project was carried out between June and December 2015, and completed just in time for the start of Nigeria’s peak season. The benefits are already apparent: “We have higher throughput, significantly reduced losses, a marked decrease in fuel consumption and maintenance costs, lower effluent production and greenhouse gas emissions, and better control over the entire process.”
High expectations fulfilled
TCS was called in by Siat for the construction of the steel superstructure at the Presco PLC plant. “We had high expectations for this work because we needed more than just a steel constructor,” says Anthony Cornelius. “We needed a company with extensive engineering expertise because we knew our early design was not really mature. TCS reviewed our initial drawings and proposed a number of improvements, especially to the mobile service platform. What’s more, they delivered a flawless structure our local people were able to erect within two weeks.”
Similar projects have been carried out for Siat in recent years in Nigeria and Ghana. One project in Ghana was the construction of a steel structure around a new steam boiler at the GOPDC plant. Koen Van Boxstael, Senior Purchaser at Siat, elaborates: “We asked several firms to tender for this project. TCS was one of them, and they have already really surprised us even at the presales stage. They had evaluated our design and proposed an alternative that would better serve our purpose, while also being compliant with European standards such as EC3 and EN1090. We very much appreciated that.”
Specifications
Projects in Nigeria:
- Construction of a 386 m² building with an 11.3m ridge height, made of 25,078 kg structural steel and 9759 kg platforms and guard-rails.
- Construction of a 660 m² building with a 21m ridge height, made of 47,140 kg structural steel and 29,928 kg platforms and guard-rails.
- Construction of 185 m² of platforms, totalling 28,496 kg of steel.
Project in Ghana:
- Construction of a 351 m² building with a 20.2m ridge height, made of 53,605 kg structural steel.