Turnkey contractor reduces project risks
LSC took no risks for the construction of its new service centre in Bree. “Our turnkey contractor had optimized the plant layout,” says Edwin Cramer. Nevertheless, a number of site-related issues required special attention when works started. Thanks to TCS’s solid expertise and good planning, the works were completed in about 15 months.
TCS designed an efficient factory layout on the 37,000 m² grounds at the Zuid-Willemsvaart. “It’s comforting to know that they have expertise in both crane and building construction,” says Edwin Cramer. “This way, they could optimize all aspects of the building, including steel structure, foundations and crane infrastructure. I only had to communicate the limiting conditions of our production process, they took care of the rest. As a result, they designed a highly optimized building in terms of feasibility and efficiency.”
Avoid costly soil consolidation
Unfortunately, once the construction works started, it turned out that, at certain points, the underground soil was too weak to support the building. “Preliminary soil sampling had not revealed this weakness,” says Edwin Cramer, “which meant that turnkey contractor TCS was forced to find an alternative for the foundations quickly. Interestingly, they proposed a solution based on gravel piles, thus avoiding a costly soil consolidation.”
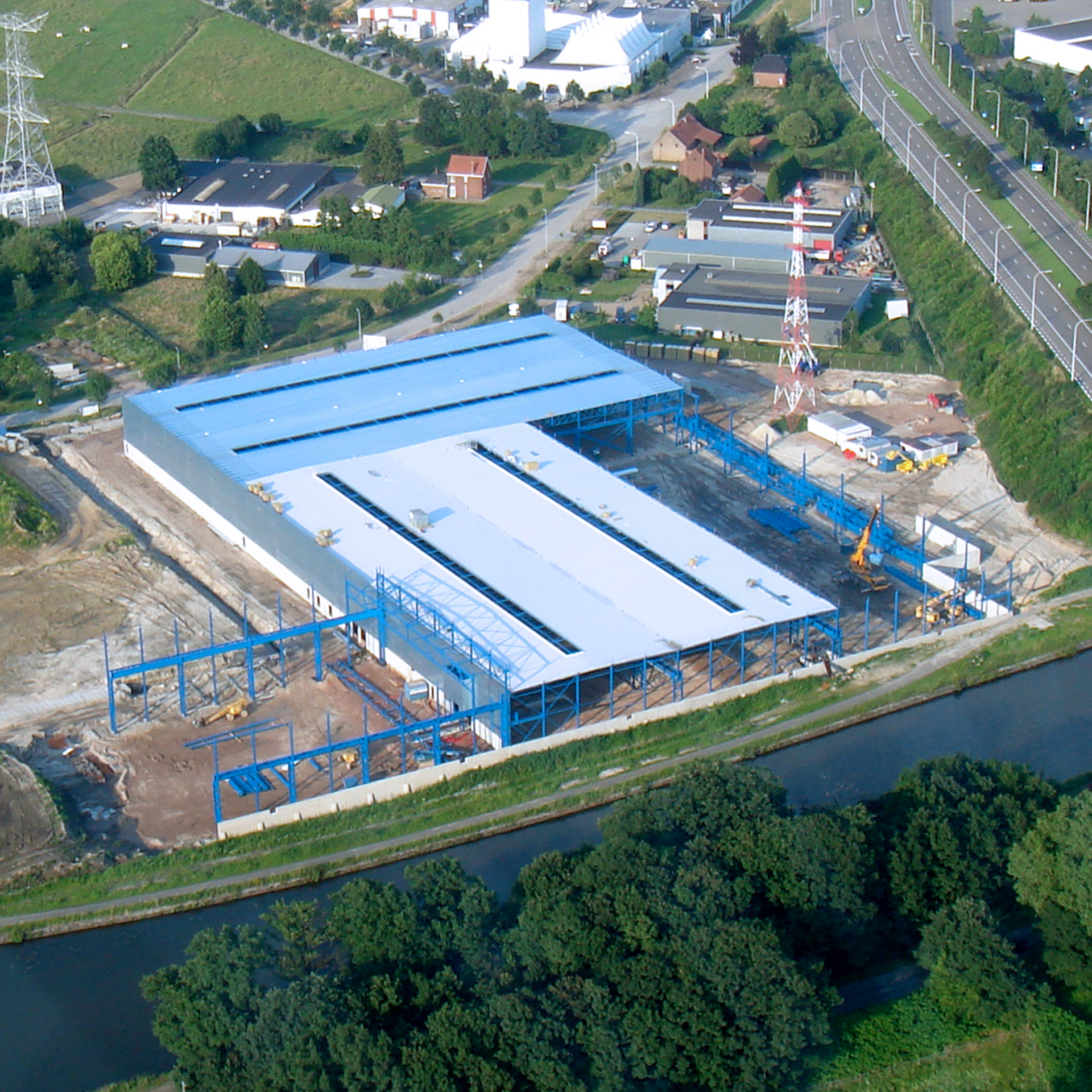
An experienced turnkey contractor
TCS also took care of all the co-ordination work required to carry out the project. Cramer: “For instance: an Elia high voltage power carrier runs over the terrain. For safety reasons, this had to be switched off during crane manipulations, requiring careful planning and co-ordination. That’s another reason why we have chosen this experienced turnkey contractor, a partner that offers much more than your typical steel constructor. This significantly reduced the hardships for us.”