Crane revamping is a growing business. There is now greater awareness among business owners that even very old portal or overhead cranes can compete functionally with new equipment when they are given an appropriate upgrade. There’s one essential prerequisite: a pro-active and flexible crane service provider.
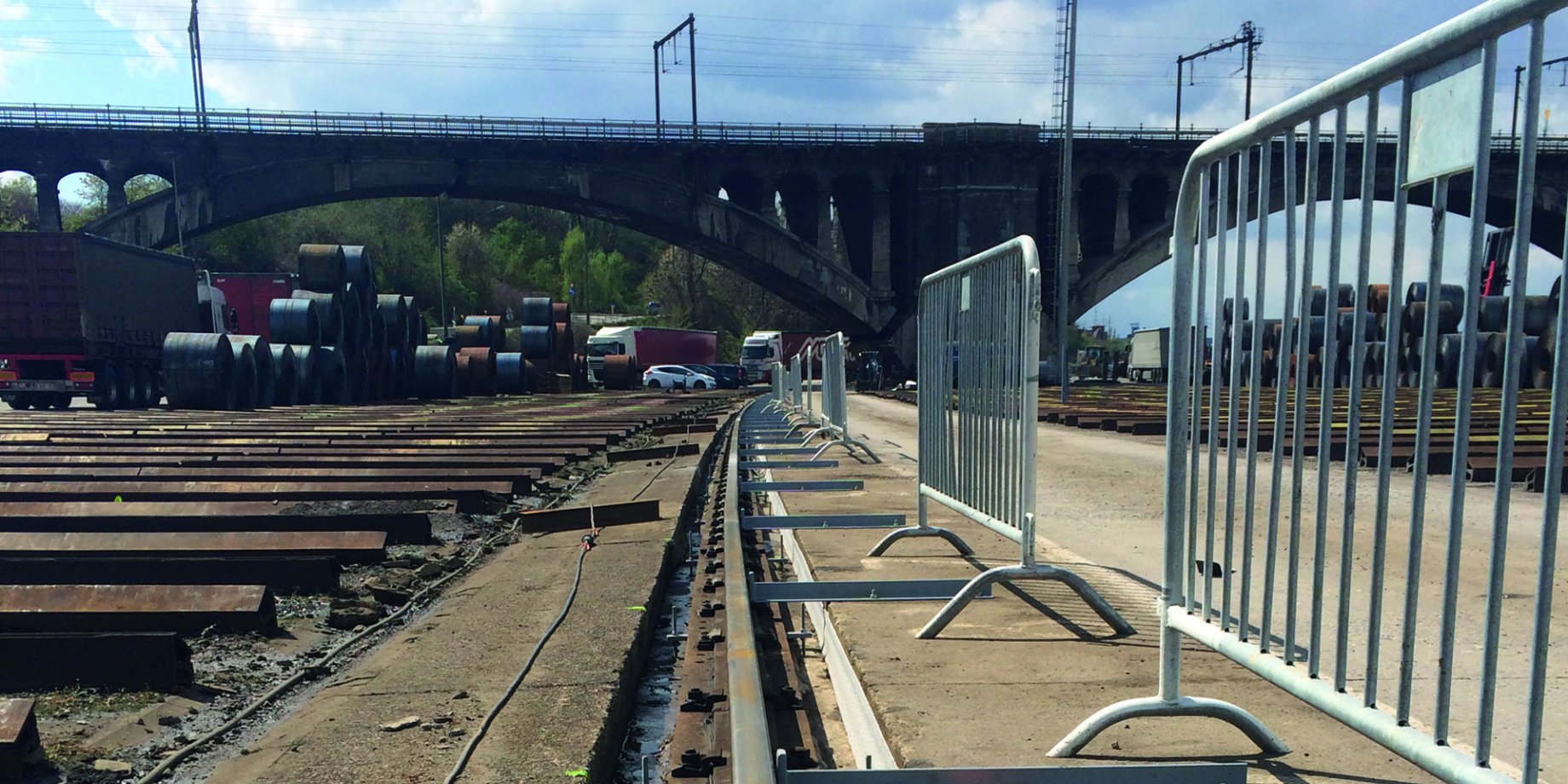
A new life for ‘grandad’
A continuous lifetime extension approach has become almost customary for newer cranes in recent years, but that was not the case for cranes installed 30 or more years ago. Many of these vintage cranes have been maintained and updated in a rather ad hoc manner with the emphasis on corrective maintenance and compliance with the latest safety standards, and less on reliability, operating comfort and long-term performance. Nevertheless, some of these older cranes are still critical for business so it is a wise move to give them appropriate attention by carrying out lifetime-extending improvements, as illustrated by some of the recent revamp projects carried out by TCS.
Beyond just problem solving
Several upgrades and improvements have been carried out on the two portal cranes owned by Port of Liège logistics operator Renory. Both had been in use since the 1980s but recently some issues had emerged, says Renory director Patrick Van Geneugden: “Crane 1’s travelling wasn’t as smooth as normal and Crane 2 made a screeching noise during operation. As part of scheduled maintenance, TCS took a closer look and found that one rail of Crane 1 had sagged a little and Crane 2’s trolley rails were completely worn-out. They warned us that both issues could lead to severe structural damage to the cranes. We therefore decided to correct the problems immediately.”
The sagged rail was taken away so that the foundations could be reinforced and levelled-out, before it was refitted and precisely re-aligned. The trolley rails of Crane 2 were replaced with new ones. In addition, a plan was made to further modernise both cranes. Electrical equipment and cabling is soon to be replaced and LED lighting will be installed to improve safety and operating comfort. “That will bring our old cranes right up to current safety, performance and reliability standards,” concludes Van Geneugden.
Eliminating worries
A slightly different story reinforced the point at Aquafin’s water treatment station in Deurne, where the electric cabling of a 1980s-era overhead travelling crane was completely worn out due to year-round exposure to a corrosive atmosphere containing methane and hydrogen sulphide. Maintenance manager Georges Peters explains: “The crane is critical for us during the plant shutdown period when it is used for maintenance. But we were increasingly worried about its poor reliability, and especially the condition of the electrical cables, which had caused a number of equipment breakdowns in recent years. Following the latest incident, we issued a request for quotation among crane service providers. TCS provided the best offer, convincing us that they would be able to replace the cabling before the crucial plant shutdown period and at the same time also upgrade the associated electrical equipment. They lived up to their promise. It is comforting to know that our old machine is now as reliable as ever.”
A plan was made to bring our old cranes completely up to current safety, performance and reliability standards
Even in difficult circumstances
Interventions have also been carried out at titanium dioxide producer Kronos Europe, in the Port of Ghent, where three 1980s-era production cranes were showing signs of severe wear and tear. Analysis revealed that one crane needed to be replaced entirely but that the two other cranes could be given an extended life with an appropriate upgrade. Project manager Filip Roelandt explains: “The structure of the cranes was found to be in good shape but some of the components needed to be replaced. Importantly, TCS proposed further modifications to bring the technology up to current standards, improve maintainability and the accessibility of critical components, and simplify problem identification. What’s more, TCS was the only company willing and able to carry out this renovation, as other firms had backed off because of the difficult assembly conditions and the tight manoeuvring space.”