Eine Vielzahl von Investitionsprojekten im Asien-Pazifik-Raum hängt noch zu einem gewissen Grad vom europäischen Know-how ab. Ulrich Beck und Jan Olhöft von Siemens bestätigen: „Für einige der anspruchsvolleren Aufgaben ist es nicht ungewöhnlich, dass wir keine zuverlässigen Partner auf dem lokalen Markt finden. Dann wenden wir uns an europäische Fachfirmen, um uns auszuhelfen.” TCS entwickelte und fertigte kürzlich einen speziellen 500-Tonnen-Kran-Testlasthalter für Siemens Energy.
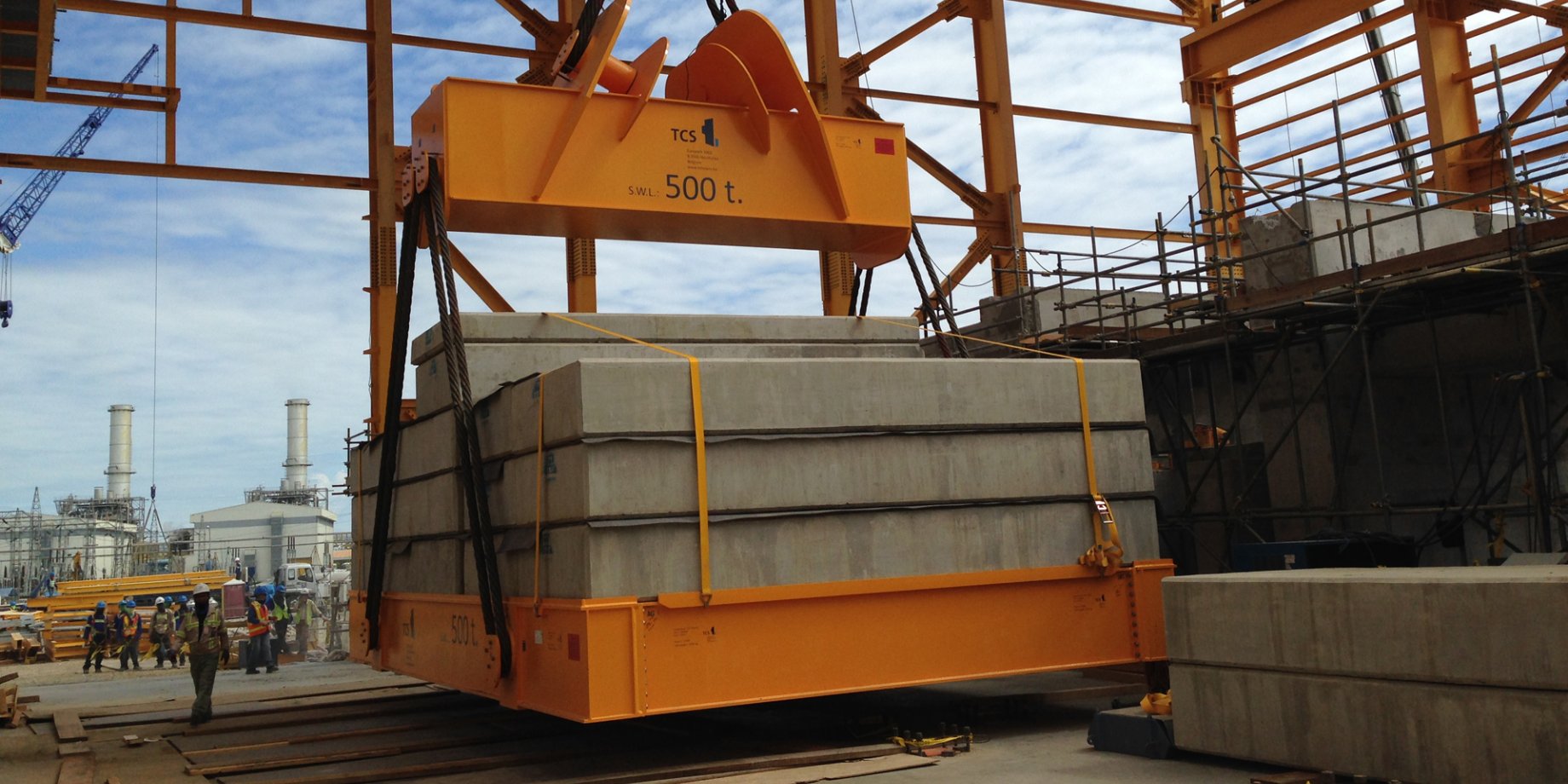
An urgent call from the Far East
Siemens ist weltweit führend in der Entwicklung moderner Energieerzeugungs-, -verteilungs- und -managementsysteme und damit auch im Asien-Pazifik-Raum sehr engagiert, insbesondere beim Bau von Gaskraftwerken zur Deckung des steigenden Energiebedarfs. Ein wesentlicher Aspekt dieser Projekte ist die Auswahl, Qualifizierung und Beauftragung leistungsfähiger Subunternehmer. „Aufgrund unserer anspruchsvollen Projektpläne bevorzugen wir den Einsatz lokaler Auftragnehmer, um Transportzeiten zu sparen und einen lokal verankerten Partner zu haben, der mit den lokalen Sicherheitsrichtlinien und benannten Stellen vertraut ist,” erklärt Jan Olhöft. „Doch das ist angesichts der hohen Anforderungen an Qualität, Kosten, Lieferzeit und technische Spezifikationen nicht immer realisierbar. In manchen Fällen ist der lokale Markt nicht in der Lage, die Anforderungen an das gewünschte Produkt zu erfüllen. Dann greifen wir auf unsere europäischen Partner zurück.”
Keine Routineangelegenheit
Manchmal treten jedoch erst dann Lücken im lokalen Lieferantenmarkt auf, wenn das Projekt bereits im Gange ist. „Es kommt vor, dass wir Angebote von mehreren lokalen Lieferanten einholen und dann feststellen, dass diese das, was wir brauchen, nicht rechtzeitig und kostengünstig liefern können. Dann müssen wir schnell handeln.”
Ein Beispiel dafür war die Konstruktion und Fertigung eines Testlasthalters, der bei der Inbetriebnahme von zwei im Bau befindlichen Kraftwerken im Asien-Pazifik-Raum eingesetzt werden sollte. Ulrich Beck erklärt: „Bei der Inbetriebnahme muss der Brückenkran in der Turbinenhalle mit einer Plattform getestet werden, die für das Heben und Transportieren von Betonblöcken mit einem Gesamtgewicht von 500 Tonnen ausgelegt ist. Da dieser Bereich von Prüflasten hohe Kräfte freisetzen kann, stehen die technischen und Sicherheitsanforderungen an erster Stelle und können das Projekt massiv gefährden. Der Testlasthalter muss nach den höchsten Spezifikationen internationaler Normen wie EN 13155, EN 3834-2, EN ISO 5817 (Klasse B), EN 10164, EN ISO 13920 und EN ISO 8501 konstruiert und gefertigt werden. Das ist sicherlich keine Routineangelegenheit.” (siehe „Anforderungen an die Testlasthalter“).
Sie hatten nur drei oder vier Wochen für die Produktion, mitten in der alljährlichen Hektik vor dem Sommerurlaub
Versprechen einhalten
Zunächst behaupteten einige Stahlbauer im Asien-Pazifik-Raum, eine solche Plattform bauen zu können, doch das stellte sich als falsch heraus. Ulrich Beck: „Bei der Planung der damit verbundenen Aktivitäten gaben diese Unternehmen an, dass sie nicht über das Know-how verfügten, um einen solchen Testlasthalter zu entwerfen. Also wandten wir uns schnell an TCS in Belgien, um sie zu entwerfen und zu entwickeln. Später erfuhren wir auch, dass kein lokales Unternehmen über die erforderlichen Zertifikate zur Herstellung der Plattform verfügt. Also kamen wir zurück zu TCS und ließen sie die Plattform bauen.”
Das bedeutete, dass wir keine Zeit verlieren durften. „Bedenken Sie, dass der Transport von Ausrüstungen von Europa in den Asien-Pazifik-Raum sechs bis acht Wochen dauert,” sagt Olhöft. „Da die Tests ab November 2014 geplant waren, verlangten wir von TCS eine Lieferung Ende Juni. Das ließ ihnen nur vier Wochen für die Produktion, mitten in der alljährlichen Hektik vor dem Sommerurlaub. Aber wir wussten von früheren Aufträgen, dass sie uns nicht im Stich lassen würden. Und wieder einmal hielten sie ihr Versprechen ein.”
Anforderungen an die Testlasthalter
Das Design und die Konstruktion des Testlasthalters sind für einige spezifische Herausforderungen vorgesehen:
- Die Struktur einer solchen Plattform muss statisch bestimmt werden, da sie an 4 Punkten angehoben wird.
- Sie sollte mit einem Doppellasthaken mit Hakengrößen von 40 bis 100 mm angehoben werden können.
- Das Stapeln der Lasten muss einfach und sicher sein.
- Aus Transportgründen musste der Testlasthalter demontierbar sein, daher die Entscheidung, eine verschraubte Plattform zu bauen. Um die massiven Zapfen mit 200 mm und 400 mm Durchmesser ohne Schweißen befestigen zu können, war eine intelligente Konstruktion erforderlich.
- Die Konstruktion musste so ausgelegt und berechnet werden, dass die Verwendung von minderwertigem Stahl (S235) und minderwertigen Schrauben (4.6) möglich ist, unter der Annahme, dass die Fertigung in Fernost stattfindet, wo höhere Qualitäten nicht leicht verfügbar sind.
Spezifikationen
- 10,25 m x 6,6 m x 8,0 m Stahl-Testlasthalter zum Stapeln von Prüfgewichten.
- Die Eigenlast beträgt 51,5 Tonnen, einschließlich zwei Kabeldurchführungen mit Ø 120 mm und drei mit Ø 96 mm.
- Die Nutzlast beträgt 500 Tonnen, jede Kabeldurchführung mit Ø 120 mm hat eine Kapazität von 333 Tonnen und jede Kabeldurchführung mit Ø 96 mm hat eine Kapazität von 178 Tonnen.
- Die Prüfgewichte sind Betonblöcke von 2 m x 6 m mit einem Gewicht von je 20 Tonnen.
- Maximale Konfiguration: 5 Lagen von je 5 Blöcken.